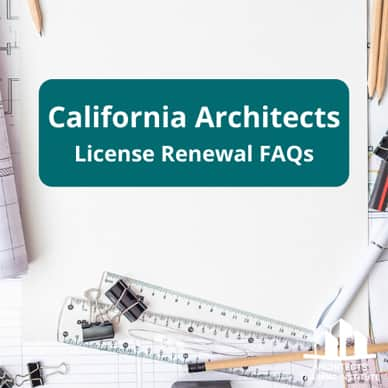
California Architects License Renewal FAQs
Published on April 26, 2023 by Nate Bortz
Here's how to renew your California architects license, and information on where to find state & AIA approved continuing education courses.
Published on April 26, 2023 by Nate Bortz
Here's how to renew your California architects license, and information on where to find state & AIA approved continuing education courses.
Published on November 19, 2021 by Betty White
You can work as an architect virtually anywhere, but some cities offer better opportunities than others. Let's see what those cities are!
Published on October 7, 2021 by Betty White
One of the most important skills an aspiring architect needs is efficient time management. With this in mind, here are a couple tips on how to work smarter, not harder, as an architect.
Published on September 14, 2021 by Nate Bortz
Architecture firms across the country are reevaluating their fall plans to return to their offices. Learn more about how firms are responding to remote work, and about the possible long-term remote work benefits.
Published on September 3, 2021 by Nate Bortz
Architects Training Institute (ATI) is happy to announce that it will now distribute OSHA 10 & 30 Hour Outreach online training course programs!
Published on August 6, 2021 by Nate Bortz
With the recent economic recovery, the AIA is feeling hopeful about future construction spending and architect opportunities.
Published on June 23, 2021 by Nate Bortz
After dealing with COVID-19 for over a year, major architect organizations gathered data that reveals future post-pandemic growth opportunities.
Published on April 22, 2021 by Nate Bortz
The AIA recently released a new "career guide" for K-12 students. To help increase awareness, we made a simplified version of it that's easy to share.
Published on April 8, 2021 by Nate Bortz
This week, the American Institute of Architects announced the launch of a new initiative called Next to Lead that aims to bring more "ethnically diverse women into AIA leadership positions." Read on to learn more about this program's eligibility, and why the AIA found it necessary to create it in the first place.
Published on March 5, 2021 by Nate Bortz
Last week, President Biden revoked the "Promoting Beautiful Federal Civic Architecture" executive order. Here's what was in the order, and why it was it overturned.